Firth Industries Customer Story
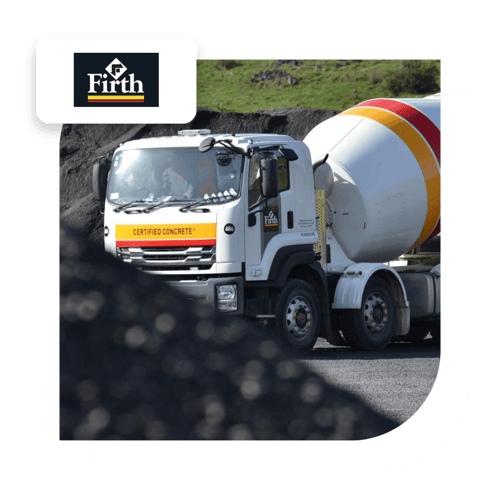
CLIENT:
Firth Industries
Firth Industries is New Zealand's largest and only national concrete company, producing ready-mix concrete, masonry, paving, retaining walls and brick veneers for commercial and residential application.

The MAX-SAFE Anti-Rollaway solution has been a major safety investment for Firth. While it is not the cheapest solution on the market, it is the best. We are on a journey to improve safety and raise industry standards and see this as a legacy project.
André van Pletzen
Head of Environment, Health, and Safety, Fletcher Building Concrete Division
Snapshot
New Zealand concrete giant, Firth Industries, is installing the MAX-SAFE Maximum Safety Anti-Rollaway Brake™ Solution to provide world-class safety on over 350 concrete trucks.
The innovation was chosen after Firth’s Health, Safety, Environment and Sustainability (HSE) team, led by André van Pletzen, conducted an extensive evaluation of rollaway safety offerings from ANZ, Asia and the UK.
With diverse fleet dynamics (manual, automatic, fuel and ev), the company is aiming to remove heavy vehicle rollaways as a safety risk for their business.
While Firth has had no major injuries due to heavy vehicle (HV) rollaway incidents, there have been several HV rollaways accidents across New Zealand in recent years.
With safety as a core priority, Firth wanted to adopt a proven safety solution to prevent vehicle rollaways – caused by operator error or faulty park brake systems – to keep staff, contractors and the general public safe.
Read on for details on:
- The business overview
- The safety challenge
- The hunt for an anti-rollaway solution
- The rollout
- Outcomes & value
- Key benefits
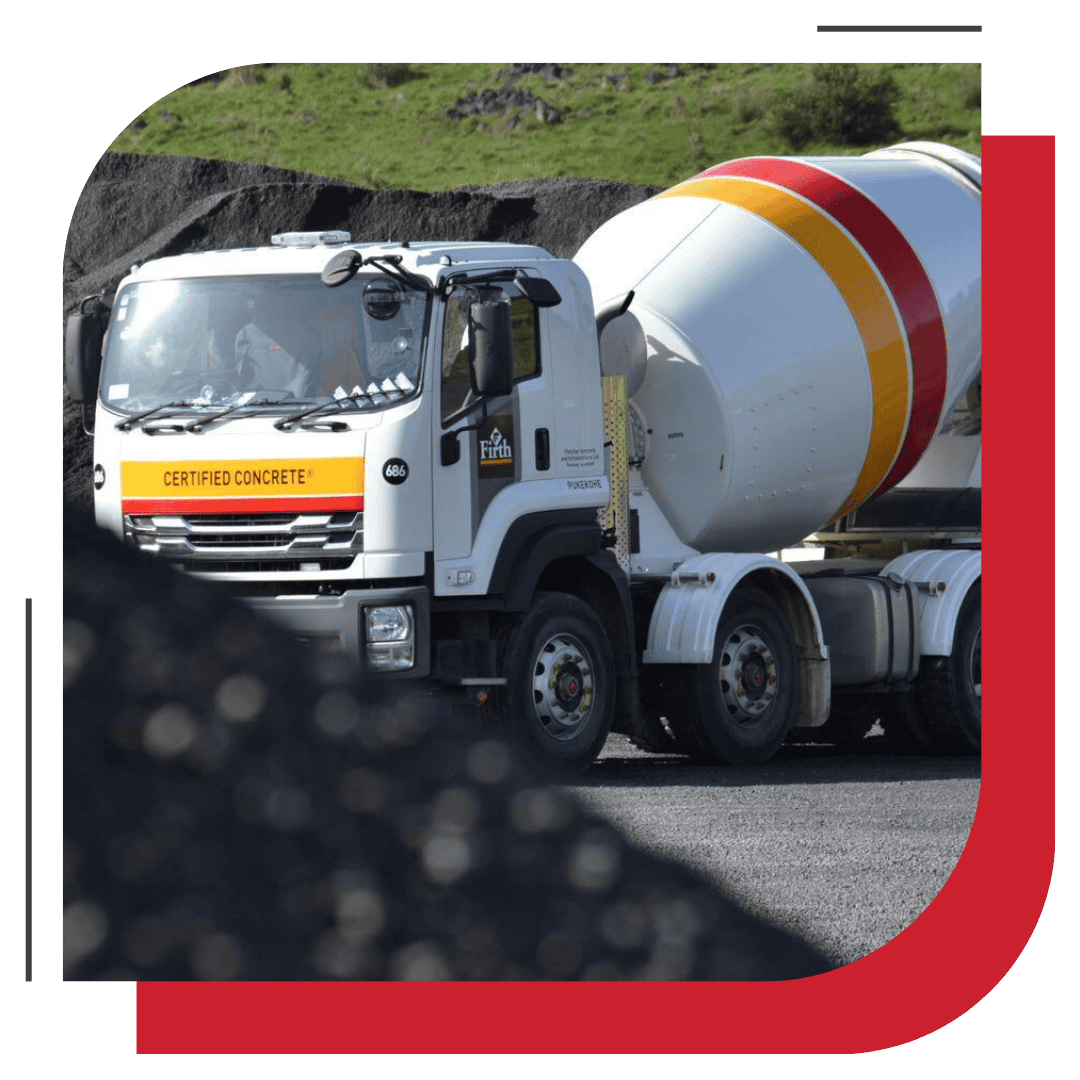
-
Business Overview
Firth Industries, a division of Fletcher Building Concrete, has been developing, manufacturing and delivering concrete and concrete products in New Zealand for almost a century.
Employing over 700 people across 72 plants throughout New Zealand, Firth Industries has a fleet of approximately 250 vehicles with another 100 owner-driver sub-contracters that carry Firth concrete bowls. At times, these vehicles can be used around the clock, with drivers working different shifts to support customer project requirements such as deadlines, operational consenting, as well as other variables such as traffic and weather.
With safety, innovation and environmental sustainability as key company values, in 2020 Firth started transitioning its fleet to newer, lower emission vehicles.
As of 2024, 30% of their fleet are less than three years old, with more automatic HVs entering the fleet as well as New Zealand’s first 8-wheeler EV (Electronic Vehicle) concrete truck based at their Manukau plant. The remaining 70% (approximately 200 HVs) are less than 10 years old. The company has also invested in developing a NZ-built hybrid concrete truck that’s based on a diesel truck fitted with a fully electric concrete bowl.
-
The Safety Challenge
Following various significant roll-away incidents in the wider NZ trucking industry, Firth decided to review the risk the business faced. Firth has experienced drivers, however with an increase in a variety of vehicles (manual, automatic and EV) that drivers were using, this heightened the risk of human error. Even the most experienced drivers can inadvertently improperly apply a parking break when regularly changing vehicle types, leading to unintentional vehicle movements.
While manual drivers were accustomed to ensuring the vehicle was in gear and the parking brake was applied before exiting, automatic vehicle drivers could easily forget to apply the parking brake after selecting neutral.
To mitigate this risk, Firth sought a robust engineering solution that would prevent unintended vehicle movement, even if the parking brake was not applied or applied incorrectly. While existing audio alarms had proven effective in preventing multiple incidents, a more reliable and proactive approach was deemed necessary.
-
The Hunt for an Anti-Rollaway Solution
In 2020, Firth’s head office established a relationship with the MAX-SAFE Distributor for New Zealand, Autokraft Electrical and Diesel (AED), after Firth’s Hamilton Depot Manager, John Hardisty, came across the anti-rollaway solution on a local heavy vehicle.
Firth has always installed park brake alarms in their vehicles but was wanting to find a solution that was failsafe and could automatically engage a vehicle's park brake if it had not been activated.
The MAX-SAFE Maximum Safety Anti-Rollaway Solution was an Australian invention, in use for over 20 years, that prevented rollaway vehicles – forward or backwards – irrespective of slope or idle creep – providing driver and company surety.
After being introduced to this solution by AED, André decided to explore this and other suitable options to ensure the best fit for Firth’s requirements.
SAFETY THROUGH CONSISTENCY
Shortly after, a number of Firth’s newer Hino vehicles – the 500 Series – came with the option of having an anti-rollaway solution pre-installed at delivery. This anti-rollaway solution, coincidentally, happened to be MAX-Safe Anti-Rollaway.
Since then, over the past two + years, AED’s installer network has fitted this technology into all new heavy vehicles before they are added to the Firth operational fleet.
Having only new vehicles fitted with an anti-rollaway device was good, as this was an engineering control. The challenge was that the risk was only controlled through administrative controls (alarms) in the majority of the heavy vehicle fleet.
Firth wanted to ensure that there was consistency across the fleet, so drivers could have the confidence that there was an automatic braking solution in place – whether the vehicle was new or old, manual or automatic, diesel, petrol or EV. A solution that would work the same across all vehicles would be ideal.
MAX-SAFE ON ANY MAKE AND MODEL
Through ongoing discussions with AED, Firth discovered that the Hino Anti-Rollaway solution – MAX-SAFE Anti-Rollaway – could work on any make or model of heavy vehicle and be installed on new or existing vehicles.
In December 2021, Matt Rowe and Gary Puklowski, Co-Managing Directors of AED, went to Hamilton to install and demonstrate the MAX-SAFE Anti-Rollaway solution on an Isuzu vehicle. This gave André the confidence to be able to standardise on MAX-SAFE across the fleet.
-
The Rollout
The roll-out has seen MAX-SAFE Anti-Rollaway progressively retrofitted on all of Firth’s heavy vehicles, as well owner-driver vehicles. The Firth fleet consists of Isuzu, UD and Hino trucks which are in heavy use Monday to Friday.
To ensure minimal disruption to truck availability and service levels, the solution has been installed by trained AED MAX-SAFE installers and dealers on weekdays and weekends, with approximately two vehicles being able to be retro-fitted per day per installer team.
As of September 2024, 260 trucks across the country have been upgraded with this safety prevention, ensuring Firth trucks are no longer susceptible to rollaway. The final 70 trucks will be installed over the coming 10 months.
AED is project managing the roll-out in conjunction with Firth Regional HSE Advisors and Operational teams.
For each location, AED has organised installers and certifiers to manage, test and qualify the installation before the concrete truck is released back into the fleet.
MAX-SAFE has also put together an easy to use training module that is being rolled out to drivers at the same time.
According to the Firth team, “It has been a positive experience working with AED. It has been a massive task with many challenges, and communication was essential. The AED team has been professional, transparent and proactive when tasked in managing the fitout and certification process. The training module has been well received too.”
-
Outcomes & Value
According to André, Firth had a responsibility to prevent one of the most avoidable types of safety accidents which could lead to tragic consequences.
“The MAX-SAFE Anti-Rollaway Solution has been a major safety investment for Firth,” he said. “While it is not the cheapest solution on the market, it is the best.
“With our business driven by the safety of not only our people but all our stakeholders, we look for innovative approaches to support our drivers in ways that are beneficial to the business and ensure our drivers are supported to be safe.
“We are on a journey to improve safety and raise industry standards and see this as a legacy project,” André said.
-
Key Benefits
The MAX-SAFE Maximum Safety Anti-Rollaway Brake™ solution
-
Maximum safety for all people and property
-
Active, automatic system – no driver intervention, no complicated processes
-
Inbuilt algorithms for constant self-analysis for faults
-
Engineering control mitigating possible human error (neglect to apply park brake)
-
Ideal for any industry that uses heavy vehicles
-
Prevents runaway vehicles, including on steep hills
-
Out of the box customised solution with ready-to-go plugs for each vehicle type – no splicing of wires, full confidence in the integrity of the system
-
Same solution works on all vehicle types
-
Inbuilt Park brake alarm – meets site safety requirements
-
Back-up service – experienced NZ-based dealers for installation, certification and service
-
Confidence in the solution, peace of mind knowing drivers and people are safer
-
Preventative maintenance available for all MAX-SAFE solutions
- Full MAX-SAFE training modules available
With thanks to Firth Industries for provision of images of fleet vehicles.
-